蝕刻製程 ETCH
Step 1 從製程痛點出發
從製程痛點出發
蝕刻製程Etch
蝕刻(Etch)製程是半導體製造中的關鍵步驟,用於移除材料以形成所需的結構。此製程涉及化學或物理方法來選擇性地蝕刻基板上的材料。然而,蝕刻製程中存在一些常見的問題和挑戰,包括:
- 蝕刻深度不均:蝕刻過程中,氣體流量和反應條件的不均勻會導致蝕刻深度不一致,影響結構精度和性能。
- 側壁斜率問題:不穩定的蝕刻條件可能導致蝕刻側壁的斜率不符合要求,從而影響元件的功能和可靠性。
- 材料殘留物:蝕刻過程中可能留下殘留材料(如碳化物或未完全去除的材料),這些殘留物會影響後續製程或導致品質缺陷。
- 化學品控制:化學品的純度和流量會影響蝕刻效果,造成蝕刻不均或不完全,進而影響最終產品的質量。
- 結構損傷:過度蝕刻或不均勻蝕刻可能損壞基板結構,導致製程失效或產品性能下降。
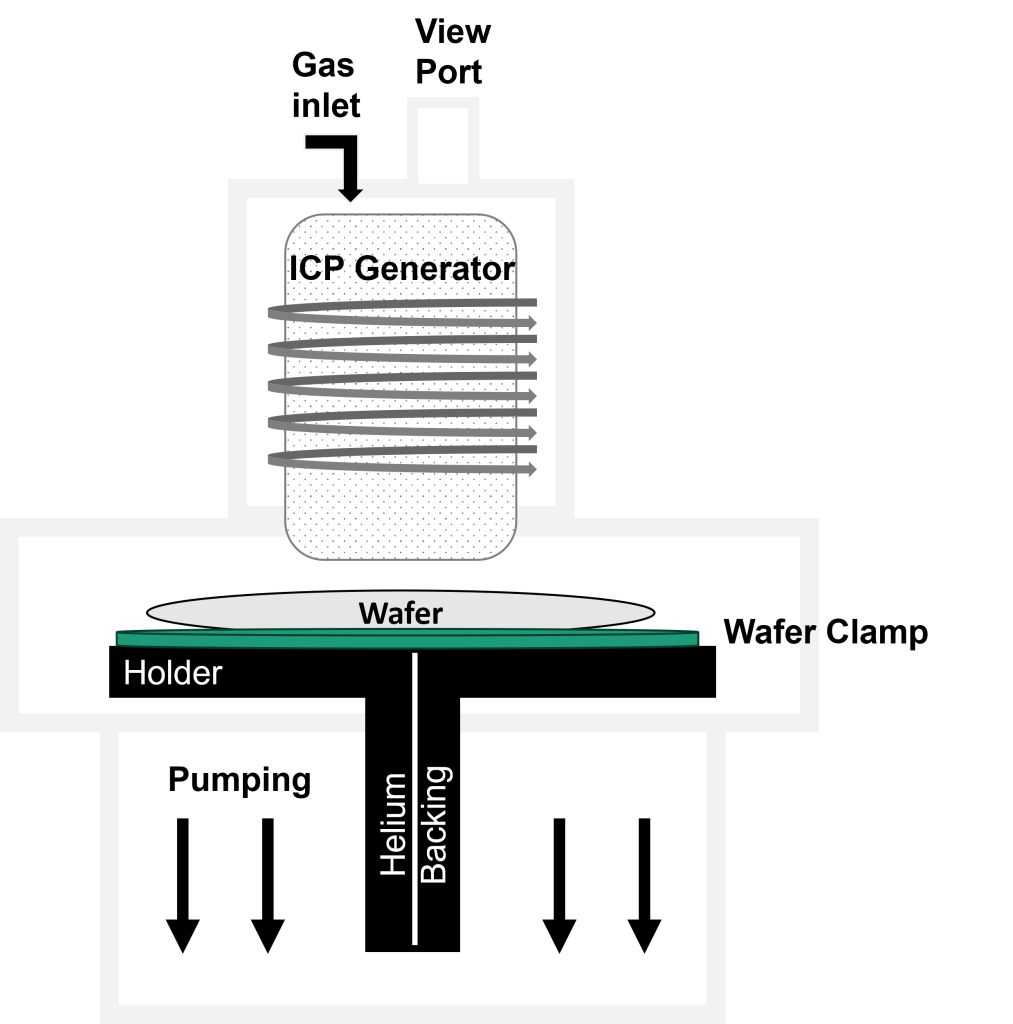
Step 2
建立檢測手法並取得數據
在蝕刻製程中,許多零配件直接影響蝕刻效果和最終產品的質量。為了確保蝕刻過程的穩定性和精確性,我們協助客戶對重要零配件進行詳細的物理性質檢測。例如,靜電吸盤的靜電吸附力對防止晶圓移動或晃動至關重要,因此針對該零件進行全面品質檢測,從而確保蝕刻過程的精準性和均勻性。
Step 3
零件檢測數據可視化 | 電子化履歷
將關鍵檢測結果分析與收集,並運用SPC手法,顯示多樣量測數據的變異性,找出零件品質規範上下限(UCL / LCL)。通過電子化履歷數據的趨勢分析,以數據驅動的方法來管理和提升零件的品質。如果發現趨勢顯示零件品質逐漸偏離設定的上下限,我們可以及時幫助客戶發現並調整零配件品製,以保持產品品質的穩定性。

客戶見證效益
- 提升ETCH蝕刻製程的穩定性和可靠性
- 確保零配件性能與穩定性
- 降低因零配件品質問題導致的製程中斷風險,提高生產效率
- 減少由於不良零配件導致的晶圓移位或損傷,進而降低製造廢品率和重工成本